Характеристика процесса сорбции в условиях Аксуской Золотоизвлекательной Фабрики
СОДЕРЖАНИЕ
ВВЕДЕНИЕ 10
1 ОБЩАЯ ЧАСТЬ 12
1.1 Краткая характеристика объекта 13
1.2 Сырьевая база, характеристика сырья номенклатура, качество и технологический уровень продукции 14
1.3 Технология производства кучного выщелачивания 18
1.4 Режим работы участка 22
1.5 Исследования руд на обогатимость 22
2 СПЕЦИАЛЬНАЯ ЧАСТЬ 24
2.1 Технологический режим участка кучного выщелачивания 24
2.1.1 Подготовка исходного материала. 24
2.1.2 Рудоподготовка сырья 25
2.1.3 Подготовка площади КВ 27
2.1.4 Отсыпка штабеля 30
2.1.5 Орошение штабеля выщелачивающим раствором 31
2.1.6 Расчет количества цианида, необходимого для выщелачивания 32
2.1.7 Обустройство системы сбора и хранения продуктивных и оборотных растворов 35
2.1.8 Цикл извлечения металла из продуктивных растворов 36
2.1.9 Описание основных технологических процессов 38
2.2 Расчет технологической схемы 43
2.2.1 Расчет количества растворов, водный баланс 43
2.2.2 Количество материала, необходимого для обеспечения выпуска металла за цикл 43
2.2.3 Количество растворов, подаваемых на штабель за сутки 45
2.2.4 Средний водный баланс 45
2.2.5 Баланс воды 46
2.2.6 Определение требуемого количества кислорода при кучном выщелачивании забалансовой руды месторождения Аксу 46
2.2.7 Расчет требуемого количества кислорода 47
2.2.8 Выбор и расчет технологического оборудования 48
2.2.9 Расчет производительности 49
2.2.10 Выбор и расчет грохота для предварительного грохочения второй стадии дробления 50
2.2.11 Расчет и выбор типа грохота для предварительного грохочения третьей стадии дробления 51
2.2.12 Выбор и расчет пластинчатого питателя 52
2.2.13 Расчет конвейеров 52
2.2.14 Выбор окомкователя 58
2.2.15 Расчёт количества сорбционных колонн, необходимых для технологического процесса, схемы их подключения 59
2.2.16 Опробование, автоматизация и контроль процесса кучного выщелачивания 60
3 ТЕХНИКО-ЭКОНОМИЧЕСКАЯ ЧАСТЬ 62
3.1 Технико-экономическая характеристика основных фондов 62
3.1.1 Организация производства во времени 63
3.1.2 Организация заработной платы 65
3.1.3 Организация ремонта 65
3.2 Технико-экономические показатели 66
3.3 Планирование производства 67
3.3.1 Планирование капитальных вложений (сметная документация) 68
3.3.2 Планирование производственных запасов 68
3.3.3 Планирование энергоресурсов 69
3.3.4 План по труду 70
3.3.5 План по заработной плате 71
3.3.6 Планирование себестоимости 74
3.3.7 Планирование дохода (прибыли, рентабельности) 76
3.3.8 Финансовый план 77
3.3.9 Расчет NPV с процессом агломерации 78
3.3.10 Экономическая оценка вариантов проектных решений 80
3.3.11 Хозяйственно-финансовый план 81
3.4 Расчет заземления 83
3.5 Потребность в энергоресурсах 85
4 МЕРОПРИЯТИЯ О ТЕХНИКИ БЕЗОПАСНОСТИ И ОХРАНЕ ОКРУЖАЮЩЕЙ СРЕДЫ 87
4.1 Общие требования безопасности 87
4.2 Охрана атмосферного воздуха 91
4.3 Противопожарные мероприятия 92
4.4 Снижение производственных шумов и вибраций 92
ЗАКЛЮЧЕНИЕ 94
СПИСОК ИСПОЛЬЗОВАННОЙ ЛИТЕРАТУРЫ 97
ПРИЛОЖЕНИЯ
ВВЕДЕНИЕ
Настоящая работа выполнена после окончания преддипломной практики которую я проходила в АО «ГМК Казахалтын» на участке кучного выщелачивания.
Я выбрала этот участок так как в последние тридцать лет наиболее динамична развивающейся технологией в сфере золотодобывающей промышленности стало кучное выщелачивание (КВ). Кучное выщелачивание золото цианированием впервые было предложено в 1967г., Горным Бюро США. Первое промышленное использование кучного выщелачивания относится к концу 60-х годов, когда компания «Карлин Голд Майнинг» на выявленном ею золоторудном поясе Карлин Тренд (штат Невада) организовала крупные полевые эксперименты. Первую крупномасштабную отработку с выщелачиванием 2млн. т бедной руды провела компания «Кортез Голд Майнз» в начале 1970г. в районе Кортез Тренд (штат Невада).
Высокие темпы наращивания золотодобычи на предприятиях достигнуты благодаря постоянной инженерно-экономической оценке сырьевых ресурсов, технически грамотному и оперативному проведению исследовательских работ, а также постоянному совершенствованию оборудования и технологии процесса КВ. За время прохождения практики передо мной стояли важные задачи по изучению технологии и поэтапных процессов выщелачивания золота из руды, а именно таких технологических процессов как:
- рудоподготовка, которая в зависимости от содержания золота, фильтрационных свойств, гранулометрического и минералогического состава сырья может включать дробление, грохочение, шихтовку глинистых руд со скальными породами;
- окомкование мелких и тонкодисперсных фракций;
-выбор и подготовку площадки под кучное выщелачивание (снятие плодо-родного слоя и планировка площадки);
- подготовку гидроизоляционного основания (отсыпка глины, её уплотнение, укладка полиэтиленовой пленки, отсыпка дренажного слоя, укладка коллекторов сбора продуктивных растворов);
- укладку руды в штабель (кучу); орошение рудного штабеля цианистыми растворами; собственно выщелачивание золота;
- дренаж растворов через кучу;
- накопление золотосодержащих растворов в ёмкости и их отстаивание ;
- извлечение золота из растворов; плавку осадков (цинковых, катодных);
- обезвреживание отработанных рудных штабелей (хвостов выщелачивания); рекультивацию отвалов и нарушенных земель.
Кроме этого к основным задачам относятся:
- Изучить характеристику сырья поступающего на предприятия;
- Технологический режим кучного выщелачивания;
- Опробование, контроль и автоматизация процесса;
- Выбор и расчет схем;
- Выбор и расчет необходимого оборудования;
- Изучение правил техники безопасности, охрана окружающей среды, противопожарные мероприятия, а так же действия чрезвычайных ситуаций.
1 ОБЩАЯ ЧАСТЬ
В последние годы повышение мирового спроса на золото способствует формированию значительных запасов сырья, содержащих золото. Особая роль состоит в том, что оно является валютным металлом. Примерно 20 % производственного золота используется в виде драгоценностей и получении промышленной продукции. Золото и его сплавы применяются в самолето- и ракетостроении для защиты от окисления высокочувствительных элементов; при сварке и пайке жароупорных сплавов, где требуется особо высокая практичность и неокисляемость сварочных швов; в ракетах, реактивных двигателях, ядерных реакторах, сверхзвуковых самолетах, космических аппаратах и др. Широко применяются покрытия из золота в электротехнике и электронике, при изготовлении различной радио- и рентгеноаппаратуры.
В настоящее время на технические цели расходуется 10-15 % добываемого золота.
1.1 Краткая характеристика объекта
УКВ, Аксуйская АЗИФ и рудник расположенный Акмолинской области в экономическом регионе. Рядом расположены предприятия ЦГХК, в 17 км находится город Степногорск.
Сырьевая база рудника слагается из месторождений «Аксу» и «Кварцитовые Горки». Отработка месторождений осуществляется подземным способом. Среднее содержание золота в товарной руде около 4.2 г/т. Кроме того, в пределах Аксуского рудного поля и вне его имеется ряд приповерхностных рудопроявлений, локализованных в корах выветривания, с содержанием золота до 2,5г/т. Эти руды могут отрабатываться карьерным способом. К сырьевой базе следует отнести лежалые хвосты обогащения (5,9млн. тонн со средним содержанием золота 1г/т). Рудник «Аксу» расположен в Акмолинской области (республика Казахстан). В состав рудника «Аксу» входит подземный комплекс, состоящий из нескольких шахт и обогатительной фабрики с флотационной схемой извлечения золота.
1.2 Сырьевая база, характеристика сырья номенклатура, качество и технологический уровень продукции
К минеральному сырью, наиболее пригодному для переработки методом КВ, относится сырьё, обладающее достаточной пористостью и проницаемостью, обеспечивающими доступ цианистых растворах к поверхности благородных металлов и диффузию растворённых цианистых комплексов металлов и продуктивный раствор КВ, который в дальнейшем поступает на извлечение благородных металлов известными методами.
1.3 Технология производства кучного выщелачивания
Расширение добычи благородных металлов во всем мире в значительной степени происходит за счет, бедных руд, как новых месторождений, так и руд эксплуатируемых месторождений (из забалансовых участков и отвалов). Рентабельное промышленное использование указанных сырьевых источников стало возможным благодаря совершенствованию технологии переработки сырья, внедрению новых способов переработки. для переработки бедных серебро- и золотосодержащих руд решающим оказалось внедрение метода кучного выщелачивания.
Кучное выщелачивание - гидрометаллургический процесс, при котором производится растворение (выщелачивание) полезного компонента химическими растворами.
1.4 Режим работы участка
График работы дробильной установки на участке кучного выщелачивания месторождения Аксу будет протекать девять месяцев в году с марта по ноябрь. График выщелачивания происходит круглогодично.
График работы дробильной установки:
12 часов в смену; 2 смены в сутки; 270 дней в году.
График работы установки выщелачивания:
12 часов в смену; 2 смены в сутки; круглогодично.
1.5 Исследования руд на обогатимость
Исследовательские работы были проведены в виде тестов в цианидных щелочных колоннах. Были взяты 3 образца руды. Все образцы были передроблены до крупности 19 мм. Извлечение золота при тестировании трех колонн составило в среднем 84,6 и колеблется от 64,9 до 95,8 %. Самое низкое извлечение золота было достигнуто от образца, в котором было самое низкое содержание (образец № 3). Извлечение серебра из трех типов составило в среднем 34,5 и колебалось от 33,3 % до 35,9 %. Самое низкое извлечение серебра было достигнуто из образца, который имел самое низкое содержание (образец № 3).
2 СПЕЦИАЛЬНАЯ ЧАСТЬ
2.1 Технологический режим участка кучного выщелачивания
2.1.1 Подготовка исходного материала
Обычно руды, пригодные для кучного выщелачивания, находятся в окисленной форме. В зависимости т комплексов, в которых удерживаются благородные металлы, руда требует такого измельчения, чтобы частицы металлов могли контактировать с раствором и эффективно переходить в жидкую фазу. Предварительная подготовка включает в себя дробление, агломерация (для мелкодробленых руд) или только агломерация (для хвостов). В отдельных случаях, выщелачивание может осуществляться без какой либо предварительной подготовки из руд забойной крупности.
2.1.2 Рудоподготовка сырья
Исходная крупность руды в питании операции рудоподготовки – минус 400 плюс 0 мм. Руда с карьера автомашинами КрАЗ (грузоподъемность 11 т) в зимнее время, доставляется на склад, в летнее время руда с карьера автомашинами и руда со склада фронтальным погрузчиком доставляется в приемный бункер питателя BW 100-6( поз.1 ), с помощью которого она подается в щековую дробилку крупного дробления ЩДП 900*1200 (поз.2). Дробленая до крупности минус 80 мм руда конвейером (поз.3) подается на грохот 2YK-2145 (поз.4 ), откуда надрешетный продукт класса минус 80 плюс 40 мм конвейром (поз.3) подается на конусную дробилку среднего дробления КСД 1200 (поз.5), а подрешетный продукт класса минус 40 плюс 15 мм конвейером (поз.3) подается на конусную дробилку мелкого дробления КМД 1750 (поз.6).
2.1.3 Подготовка площади КВ
Основные требования к площадке - она должна оставаться непроницаемой в течение всего периода эксплуатации полигона и дополнительного времени, необходимого для «жизни» штабеля на стадии его обезвреживания химическими способами или же за счет естественного разложения оставшегося цианида. Помимо хорошей изоляции, основание площадки должно обеспечивать стабильность и устойчивость фундамента отсыпанной горной массы в течение всего периода эксплуатации и так же представлять прочную основу при сооружении и формировании штабеля.
2.1.4 Отсыпка штабеля
Формирование штабеля может совершаться разными способами (от использования грейдеров до засыпки конвейерными механизмами), а это, в свою очередь, зависит от физических свойств руды. Требования к методу сооружения штабеля — исключить сегрегацию частиц при отсыпке, т.е. получить максимальную гомогенность для просачивания растворов, по возможности ограничить уплотнение горной массы при сооружении, обеспечить защиту непроницаемых пленок или прокладок в основании штабеля.
2.1.5 Орошение штабеля выщелачивающим раствором
Основное требование к стадии орошения - равномерное распределение выщелачивющего раствора по всей поверхности штабеля. Обычно выщелачивающий раствор перекачивают на верхнюю часть штабеля с помощью насоса для обеспечения достаточного давления на распылители (разбрызгиватели). На ряде рудников в качестве метода подачи растворов используют прудки, сооружаемые на поверхности отсыпаемой горной массы.
2.1.6 Расчет количества цианида, необходимого для выщелачивания
NaSCN (81,08*0,0035):159,15 = 0,0018 т
NаОН (2*40*0,0035):159,15 = 0,0017 т,
где 159,15— молекулярная масса Cu2O
187,54 - молекулярная масса Na2Cu(CN)3
81,08 - молекулярная масса naSCN
2. Сu2O степень растворения 10 %. Переходит в раствор С2O
0,071*0,1 = 0,0071 т.
Реакция:
2.1.7 Обустройство системы сбора и хранения продуктивных и оборотных растворов
Системы сбора и хранения этих двух разных по содержанию полезного компонента растворов имеют много общего. В обоих случаях используются одна и та же система гидроизолирующих покрытий, обеспечивающая полную сохранность растворов, причем в случае продуктивных растворов она должна предотвратить возможные потери ценного компонента и предупредить загрязнение растворителем окружающей среды. В случае оборотного надежная изоляция прудка требуется для исключения опасности для окружающей среды, вызываемой утечкой растворов.
2.1.8 Цикл извлечения металла из продуктивных растворов
В настоящее время практически повсеместно используется два способа извлечения золота из продуктивных растворов: способ цементации цинком (метод Мерил-Кроу) и адсорбция на угле или синтетических смолах. Первый из способов был разработан и внедрен практически с процессом цианирования в 90-х годах прошлого столетия. Существо метода цементации сводится к обработке продуктивного золото-, серебросодержащего предварительно деаэрированнного раствора цинковой пылью.
2.1.9 Описание основных технологических процессов
Руда будет транспортироваться на рудный штабель серией передвижных конвейеров, и укладываться на него с помощью радиального укладчика. Укладочные конвейеры будут транспортировать руду по длине площадки, где она будет выгружаться на радиальный укладчик. Укладчик будет укладывать руду на восьмиметровые подъемы, отступая по площадке после завершения укладки каждой очередной арки.
2.2 Расчет технологической схемы
2.2.1 Расчет количества растворов, водный баланс
Определение площади полива штабеля и объёма подачи раствора.
Цикл выщелачивания составляет: Т = 45 суток
Количество циклов для выполнения годовой программы:
310 : 45 = 7 циклов, где:
310- количество дней в году;
45 - продолжительность цикла выщелачивания сутки.
Выпуск металла за цикл:
2.2.2 Количество материала, необходимого для обеспечения выпуска металла за цикл
375 х 1000 : 2,02 = 185644 т, где:
375 - количество металла за цикл в добываемой товарной руде, кг;
2,02- содержание металла в смешанном материале, г/т.
Площадь полива штабеля при требуемом количестве руды для выпуска металла за цикл:
2.2.6 Определение требуемого количества кислорода при кучном выщелачивании забалансовой руды месторождения Аксу
Растворение золота в цианистом растворе обычно выражается уравнением Эльсинера:
2Аu + 4NaCN + Н2O + 0,5O2 = 2NaАu(CN)2 + 2NaОН (I)
Кислород необходим для ассимиляции избыточных электронов, которые накапливаются в результате перехода в раствор ионов металла.
Кислород непосредственного участия в растворении золота не принимает, но соединяясь с водородом, устраняет причину, замедляющую растворение золота. Отсутствие кислорода в растворе совершенно прекращает растворение металла, несмотря на наличие достаточной концентрации кислорода.
2.2.8 Выбор и расчет технологического оборудования
Выбор и расчет оборудования дробильного комплекса
На дробильном комплексе осуществляется подготовка руды к окомкованию и окомкование готового продукта класса - 15,0 мм.
Подготовка руды к окомкованию заключается в стадиальном дроблении и с предварительным отсевом материала готового класса.
На дробление руда поступает непосредственно с карьера, поэтому размер наибольшего куска будет примерно 600 мм. Согласно условиям проектирования, конечная крупность наибольшего куска дробленого продукта, направляемого на окомкование, составляет 15 мм. В соответствии с этими условиями принимается трехстадийная схема дробления, которая включает следующие операции:
2.2.10 Выбор и расчет грохота для предварительного грохочения второй стадии дробления
На предварительное грохочение II стадии дробления поступает 220,0 т/м3 руды с максимальной крупностью дробленого продукта - 200 мм. Размер отверстий сита грохота, согласно требованиям проекта, принят 60,0 мм.
Выбор типа грохота основывается на размере требуемой площади рассева и производительности грохота.
2.2.11 Расчет и выбор типа грохота для предварительного грохочения третьей стадии дробления
На грохот, предназначенный для предварительного и поверочного грохочения материала третьей стадии дробления, поступает дробленый продукт массой 110,0 т/час и максимальным размером дробленого продукта - 60 мм. Размер отверстий сита грохота, согласно требованиям проекта, принят 15 мм.
2.2.12 Выбор и расчет пластинчатого питателя
Руда в дробилку крупного дробления, с максимальной крупностью кусков 600,0 мм, В количестве 220,0 т/ч поступает из приемного бункера через пластинчатьий питатель тяжелого типа. Применение пластинчатого питателя позволяет устранять перегрузы или недогрузы дробилки и разгружать дробленый продукт непосредственно на конвейер.
2.2.13 Расчет конвейеров
Конвейера предназначены для транспортировки дробленой руды после I, II и III стадий дробления. Расчет конвейеров проводился по справочнику.
1. Необходимая ширина ленты - В, м
I стадия дробления: Вг = 2*D,max + 200 = 2*135*200 = 540 мм,
II стадия дробления: ВП = 2*60+200 = 320 мм,
III стадия дробления; ВШ = 2*15+200 = 230 мм
Для транспортировки дробленой руды всех стадий принимаем ширину конвейеров общую, т.е. В = 650 мм = 0,65 м
2.2.14 Выбор окомкователя
Выбор окомкователя основан на требуемом количестве рудного материала, поступающего из дробильного комплекса на окомкование, Q = 110,0 т/ч или 69,0 м3. Параметры барабанного окомкователя приняты согласно технической характеристики и приведены в таблице 10.
2.2.16 Опробование, автоматизация и контроль процесса кучного выщелачивания
В таблице представлены основные технологические параметры процесса, составленные на основе результатов научно-исследовательских работ, практики промышленной переработки золота методом кучного выщелачивания и технического задания на переработку 1 000 000 т/год руды методом кучного выщелачивания.
3 ТЕХНИКО-ЭКОНОМИЧЕСКАЯ ЧАСТЬ
3.1 Технико-экономическая характеристика основных фондов
Технико-экономическая характеристика основных фондов проектируемого дробильно-агломерационного отделения приведена в таблице 13.
3.1.1 Организация производства во времени
Организация производства во времени включает:
- режим работы;
- плановый баланс рабочего времени;
- расчет количество бригад;
- календарный график выходов.
Для проектируемого отделения получения золота, принимаем следующий режим работы:
3.1.2 Организация заработной платы
В соответствии с действующими в металлургии цветных металлов формами и системами оплаты труда в проектируемом отделении принимаем повременно - премиальную оплату труда на основании 21 разрядной тарифной сетки.
В таблице 15 приведены часовые ставки основных категорий рабочих дробильно-агломерационного отделения.
3.1.3 Организация ремонта
Основной формой организации ремонтных работ в проектируемом отделении является смешанная организация ремонтных работ, то есть часть ремонтных работ выполняется силами общезаводской ремонтной службы находящейся на участке.
3.2 Технико-экономические показатели
Технико-экономические показатели по проекту, в соответствии с инструкцией СН 202-85 сводятся в таблицу 17.
3.3 Планирование производства
3.3.1 Планирование капитальных вложений (сметная документация)
Планирование капитальных вложений в проекте представлено: объектной сметой - форма 3 по СН 202-85, по которой будет определена сметная стоимость строительства площадки для дробильно-агломерационного отделения.
3.3.2 Планирование производственных запасов
Планирование производственных запасов производим в табличной форме, представленной в таблице 19.
3.3.3 Планирование энергоресурсов
Планирование энергоресурсов производим в табличной форме, таблица 20, на основании принятой производственной программы и прогрессивных норм расхода энергетических ресурсов. Цены, тарифы принимаем с учетом действующих на момент проектирования.
3.3.4 План по труду
План по труду включает расчет численности рабочих, который производим в табличной форме, таблица 21, на основании принятых нормативов численности рабочих.
3.3.5 План по заработной плате
Планирование фонда заработной платы основных рабочих производим в табличной форме, таблица 22.
3.3.6 Планирование себестоимости
Планирование себестоимости производим в соответствии с инструкцией по планированию и калькулированию себестоимости продукции путем составления калькуляции себестоимости одной тонны руды. Расчет сводим в таблицу 24.
3.4 Расчет заземления
Исходные данные: подстанция понижающая имеет 2 трансформатора 6/10,4 кВ с заземленными нейтралями на стороне 0,4 кВ; подстанция размещена в отдельно стоящем кирпичном здании, размеры которого в плане приведены на рисунке 2.
3.5 Потребность в энергоресурсах
Электроснабжение дробильно-агломерационного комплекса предусматривается от линии электропередач. Линия электропередач 6 кВ строится на железобетонных опорах со сталеалюминевыми проводами. Низковольтные (0,4 кВ) воздушные линии в пределах промышленной зоны выполняются алюминиевыми проводами на деревянных опорах с железобетонными пасынками.
ЗАКЛЮЧЕНИЕ
По результатам выполненного дипломного проекта установлено, что при кучном выщелачивании требуются минимальные горноподготовительные работы и небольшие капитальные вложения на сооружение установок. Характерной особенностью кучного выщелачивания является получение материалов в виде осветленных продукционных растворов, а не в виде пульпы, что значительно упрощает их дальнейшую переработку, Наряду с высокой экономичностью кучное выщелачивание позволяет существенно ускорить отработку месторождений. При кучном выщелачивании конечный продукт в 1,5 - 2 раза дешевле продукта, полученного по традиционной технологии.
Поскольку в Казахстане основной промышленный тип золотосодержащих месторождений - кварцево-жильный и добыча руд в основном ведется подземным способом, широкого внедрения кучного выщелачивания с использованием стандартной технологии нельзя ожидать. Для этого процесса пригодны только окисленные руды верхних горизонтов месторождений, добываемых открытым способом, а также различные разновидности пород, содержащие благородные металлы, обладающие хорошей проницаемостью.
СПИСОК ИСПОЛЬЗОВАННОЙ ЛИТЕРАТУРЫ
1. Андреев С.Е., Перов В.А., Зверевич В.В. Дробление, измельчение и грохочение полезных ископаемых. М., Недра, 1980 г. 385 с.
2. Единые правила безопасности при дроблении, сортировке и обогащении полезных ископаемых. М., Недра, 1978 (Гостехнадзор СССР).
3. Кривцов Б.С., Руднев А.П. Техника безопасности и противопожарная защита на ОФ. М., Недра, 1973.
4. Металлургия бларородных металлов. М., Металлургия, 1987.
5. Лодейщиков В.В. Технология извлечения золота и серебра из упорных руд. Иркутск. ОЛО «Иргиредмет». 1999. — т. 1-2. 786 с.
6. Игнаткина. Технология комплексного обогащения труднообогатимых сульфидных золотосодержащих руд. // Изв. ВУЗов. Цветная металлургия. 2004, М 5.
7. Барышников М.Ф. Усовершенствование технологии переработки золотосодержащих руд и флотоконцентратов. М., Недра, 1968.
8. Пуншко А.А., Дементьев В.Е. Разработка ионообменной технологии извлечения благородных металлов и опыт внедрения на золотодобывающих предприятиях. // Цветные металлы. 2001. Х25. с.11.
9. Кудайбергенов К.К., Ставинский В.А., Кожонов А.К. Вклад горной промышленности в народное хозяйство Кыргызской Республики. //Горный журнал. 2002. Х 10. с.9-10.
10. Справочник по обогащению. Основные процессы. Т.2. 1983.
11. Мальцева Н.А. Совершенствование схемы переработки углисто-As-Au содержащей руды. // Журн. Цветные металлы. 1981, М 9.
12. Царьков. В.А. Опыт работы золотоизвлекательных предприятий мира. — М. Издательский дом «Руда и металлы», 2004-
13. Дорожкина Л.А. Мировой рынок золота в 2007-2008 гг. Информационно аналитический центр «Минерал» 2008.
14. Кучное выщелачивание золота. Зарубежный опыт и перспективы развития. Справочник // Под редакцией В.В. Карагановаи, Б.С. Уженова, Москва-Алматы, 2002.
15. Чантурия В.А., Седельникова Г.В. Развитие золотодобычи и технологии обогащения золотосодержащих руд и россыпей. Горный журнал, 1998, №5.
16. Дементьев. В.Е., Татаринов А.П., Гудков С.С. Основные аспекты технологии кучного выщелачивания золотосодержащего сырья. Горный журнал, 2001, №5
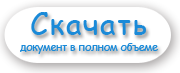